Author |
Message |
   
Rocket_in_uk
| Posted on Thursday, January 30, 2014 - 07:14 am: |
|
Jeez you're gonna use your fiance as a test pilot? Do you actually like her Rocket in England |
   
Torquehd
| Posted on Thursday, January 30, 2014 - 10:56 am: |
|
I'm not throwing her on the back until I thoroughly test it using my own weight. |
   
Rocket_in_uk
| Posted on Thursday, January 30, 2014 - 08:40 pm: |
|
Your own weight + a large backpack full of bricks Rocket in England |
   
Torquehd
| Posted on Friday, January 31, 2014 - 03:22 am: |
|
Spending the night working on the undertray model
And strengthening the subframe. The new crossbars are thinwall tube stock, and added a LOT of torsional rigidity. and i'm only up .2 lbs, now totalling 3.5 lbs. Still need to reinforce the pillion area better. And find a sacrificial oven to turn into a heat treatment facility.
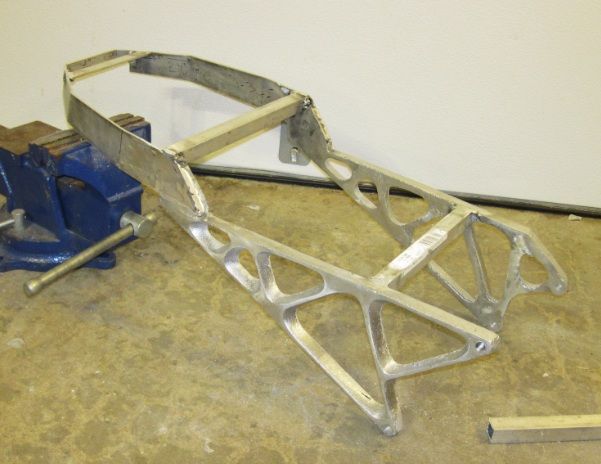 |
   
Ducbsa
| Posted on Friday, January 31, 2014 - 05:01 am: |
|
I bet some fairly shallow horizontal fins, continuous weld, on the inside of the rear section, fitted to the back plate, would do a lot of good. How much room inside that "box" can you give up? |
   
Hootowl
| Posted on Friday, January 31, 2014 - 09:51 am: |
|
Have you thought about 45 degree cross bracing? (Or some suitable angle. Triangles are strong.) Could probably get away with very small tubes. They would certainly add the rigidity you're looking for. |
   
Hootowl
| Posted on Friday, January 31, 2014 - 09:53 am: |
|
Also, the fiberglass seat pan, properly secured to the subframe, adds a whole lot of strength, I would think. |
   
Torquehd
| Posted on Friday, January 31, 2014 - 10:58 am: |
|
I was considering angular cross bracing last night for the pillion portion. In order to get the most strength, the bracing would have to go across the top of the framerails, which means the pillion "glovebox" wouldn't be as usable. So i'll try it on the bottom and see. The undertray will be carbon, so you're especially right hootowl. I had visualized the carbon as being an integral part of the frames strength, but now that it's together and I see how little room there is between the right frame rail and the shock, I don't think there's room to do what I had initially planned. However, for the pillion portion, I think an internal carbon pan would help and would add almost no weight. |
   
Hootowl
| Posted on Friday, January 31, 2014 - 02:42 pm: |
|
I was thinking the seat pan would replace the angle bracing. It would effectively be the same as nailing plywood to a 2x4 wall. They wont be able to move much once the pan is fastened to them in a couple of places. |
   
Hootowl
| Posted on Friday, January 31, 2014 - 05:38 pm: |
|
I meant the body work/tail section, not the seat pan. |
   
Ourdee
| Posted on Friday, January 31, 2014 - 08:39 pm: |
|
Seat pan? Three layers of CF sandwiched with two layers of .250" honeycomb nomex would add some safety/strength. |
   
Torquehd
| Posted on Saturday, February 01, 2014 - 04:55 pm: |
|
The newest member of the Thunderhorse Workshop family: Thunderkiln.
Craigslist special, this thing is 30+ years old. And I inadvertently bought the perfect type for heat treating: Modern kilns have three settings - low, med, high. This one has a pair of fully adjustable dials. This allows me to fine-tune the heat in the kiln.
Digital dual-thermocoupler pyrometer
This set me back a couple pennies (about 50,000 pennies altogether), but it's so worth it. Plus, I've been itching to throw pottery for a few years. Because I don't already have enough projects to overoccupy my freetime. Now it's just a small matter of experimenting on some test pieces before I throw the subframe in. The subframe is about 4" too tall to fit, so I think I'll cut off the pillion portion and reweld it after treating, since that part is stout enough and won't require heat treating. The only part I'm worried about is the long front chords of the trusses. |
   
Sifo
| Posted on Saturday, February 01, 2014 - 05:08 pm: |
|
From what I've learned about having bicycle frame repaired, welding heat treated aluminum will anneal the surrounding area creating a weak area that will lead to failure. You always had to heat treat the frame again after welding. I would be nervous about having your honey sitting on what is basically a lever that will be connected to the bike by something that is so likely to become a failure point. Results could be bad!

|
   
Torquehd
| Posted on Saturday, February 01, 2014 - 06:05 pm: |
|
Hmm... i really need to go to college for this stuff. I have a friend who is a mechanical engineer, I emailed him and I'm hoping he can give me some advice. I know that the welded portion will be weaker than the heat treated portion, but it seems hard to believe that it would be weaker than the extruded material was before it was heat treated. I'm doing a test run right now with a piece of cast, a piece of extruded, and a piece of cast welded to extruded - i'm having a hard time getting an even 1000F at both the top and bottom thermocouplers. The top is 120-140 degrees hotter than the bottom. When I turn up the heat to the bottom coils, the heat rises before it heats up the bottom, again making the top hotter than the bottom. Does anyone know (or know where to find info) about heat treating? Since the heat is rising to the top, I'm inclined to believe that without a super expensive oven, it's impossible to get even heat. I I wonder if the top can be 1050 and the bottom be 920-930... it seems like 1000 is a "magic number" so I wonder if it's just the ballpark of where the material needs to be to reach an annealed state before cold plunging. Edit: i think i know what i'm going to do, instead of cutting the pillion area off. I can unbolt the lid, stack up 2 layers of firebricks, and set the lid on top of the new layers. That will allow the whole thing to fit. It will leak some heat, but on the lowest heat setting, I have to leave the lid cracked open an inch to maintain just north of 1000 anyway. (Message edited by torquehd on February 01, 2014) |
   
Sifo
| Posted on Saturday, February 01, 2014 - 06:38 pm: |
|
I know that the welded portion will be weaker than the heat treated portion, but it seems hard to believe that it would be weaker than the extruded material was before it was heat treated. The problem is that it's weaker than the surrounding material. Now rather than have nice even flexing when it does flex, you have created a point at which it will flex. Aluminum doesn't like that for long and will stress crack. Of course, there could be spots in your design that will have that problem anyway. Or the design could also be just fine. The design could also be over built enough that welding it together after heat treating won't hurt any. All I can say is what aluminum tends to do as a material. What ever you do, I would get in the habit of checking it periodically for any signs of cracking. I'm probably being overly cautious in my advice, but it's what my lawyers tell me to do.  |
   
Torquehd
| Posted on Saturday, February 01, 2014 - 08:38 pm: |
|
haha, i didn't think lawyers would monitor your badweb postings everything is so legalistic these days. almost every day, you can turn on fox news and hear about how so and so is in trouble because he made a joke on twitter and someone got offended. facebook posts are used as concrete evidence. it's ridiculous. "survival of the fittest" needs to make a comeback, so all the morons will weed themselves out of the gene pool. Well, it was for good reason that I said earlier that 1000F sounds dangerously close to the point where aluminum gets brittle and crumbly.
This old scrap piece I cast a year ago was FLAT before. I leaned it at an angle with half of it unsupported to see if it would bend under its own weight. it did. I fired it for 2 hours at ~1000, but the kiln did get up to 1070 at one point. So, heat treating isn't the forgiving play time i wanted it to be. Prior to reaching 1070, I had periodically checked the inside when the temp never got above 1030, and it hadn't deformed at that point. I will have to monitor the temperature much more closely next time. I'm digging to find out more information before I do the actual subframe. got a couple leads on some information, i'll share once i do some more trial (and of course, error) |
   
Torquehd
| Posted on Sunday, February 02, 2014 - 12:56 am: |
|
For future reference, if anyone an Badweb ever searches for aluminum, heat treating, hardening, solution, tempering, alloy, or whatever other tags you can think of, http://www.youtube.com/watch?v=phhXy1XgLLs http://www.physicsforums.com/showthread.php?t=1333 52 http://www.alloyavenue.com/vb/showthread.php?3125-Question-on-heat-treating-castings...&highlight=machinability+aluminum I think there's enough information there to blunder your way through heat treating. I'll let you know within a week or two. (Message edited by torquehd on February 02, 2014) |
   
Bluzm2
| Posted on Sunday, February 02, 2014 - 03:58 pm: |
|
Jesse, Are you trying to stand the side castings vertically? If so, you should be able to make a removable top for the kiln that has a "penthouse" to make room for the extra length. Just fab up a frame to hold fire bricks. Leave a hole in the center and build a "house" of other bricks big enough to allow the side plate to poke through and be covered. My daughter had to do this for a sculpture she made. If the temp is below the "sag point" of the Al, you should be good. |
   
Torquehd
| Posted on Sunday, February 02, 2014 - 10:05 pm: |
|
Spent the morning doing just that, Buzm. Had to spend the afternoon with the little lady so she doesn't feel so neglected. Still need to drill a hole so I can put a pyrometer lead in the top row of bricks.
Also have some thing gauge galvanized steel cut out to wrap around the bricks, and secure with several large hose clamps. That will have to wait til tomorrow. The undertray is getting close, i think i like its aesthetics even more than the airbox cover or pillion. (Message edited by torquehd on February 02, 2014) |
   
Torquehd
| Posted on Monday, February 03, 2014 - 11:51 pm: |
|
Thunderkiln Mod II.
I've been posting on Alloy Avenue, a metal casting forum. A guy on there was nice enough to send me a PDF of all the most common Al alloys with a well of information on each. About 90% of the aluminum in all my castings comes from used Ford wheels. The vast majority of Al wheels on the market today are LM9 or LM25, both of which have a solution temp in the mid 900's (F). That explains why my test piece crumbled at 1070. M9 and M25 both respond very well to heat treating. The potential for increased tensile strength is in excess of 170% the non-treated rating. |
   
Ducbsa
| Posted on Tuesday, February 04, 2014 - 06:04 am: |
|
Is this next?
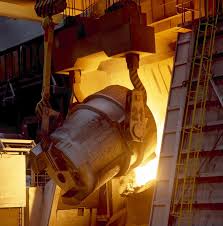 |
   
Torquehd
| Posted on Tuesday, February 04, 2014 - 10:58 am: |
|
Yeah, I'll need one of those for when I start casting adamantium. |
   
Hootowl
| Posted on Tuesday, February 04, 2014 - 11:12 am: |
|
Don't let it cool off. |
   
Torquehd
| Posted on Thursday, February 06, 2014 - 01:36 am: |
|
Went down to the Title Office yesterday and signed the paperwork on my new (to me) house. Likely going to be busy moving everything to the new house over the next 2 weeks, so I don't expect much progress on the project here soon. I've been interested in designing and making motorcycle parts for years, and I finally thought I'd found a good name. I searched high and low for "thunderhorse" and couldn't find another motorcycle related company by that name. Then I went to the USPTO website. Thunderhorse isn't registered, but Thunder horse is. Dang the luck. Oh well. I guess, by the time I go to school to get an engineering degree, I'll probably have moved on to something bigger and better anyway. |
   
Torquehd
| Posted on Friday, June 06, 2014 - 12:59 am: |
|
Well gents, part of me feels bad for not checking in, in so long. Since my last posting, I moved into the new house, had a short deployment to SE Asia, have been planning (and paying for) a wedding, have been working on moving my fiance's 7 year old son in with us and adopting him as my own, started a garden, built a chicken coop, built a duck coop, built rabbit cages, spent a week rock climbing in central Washington.... I have been busier than a one-armed cowboy riding full tilt in the wind, trying to roll a cigarette. The Thunderhorse project has been suspended for an indefinite amount of time. I hope to get back on the 'horse this fall, but that will remain to be seen. Knowing that I still have a couple hundred hours worth of work ahead of me, I opted to put the stock tail section back on so I can ride the bike this summer. The swap took less than an hour, which was nice. I've had this bike for about 3 years now, it's my third Buell, and I am still in love with it. There's something nice about coming back after not riding for months on end. It helps me have an appreciation for the amount of power this thing makes, the smooth, precise torque curve, the fine handling. It's a beautiful machine and I thank God that He's blessed me with one. |
|