Author |
Message |
   
Truckinduc
| Posted on Sunday, December 28, 2014 - 02:00 am: |
|
Here is the spacer going back in.
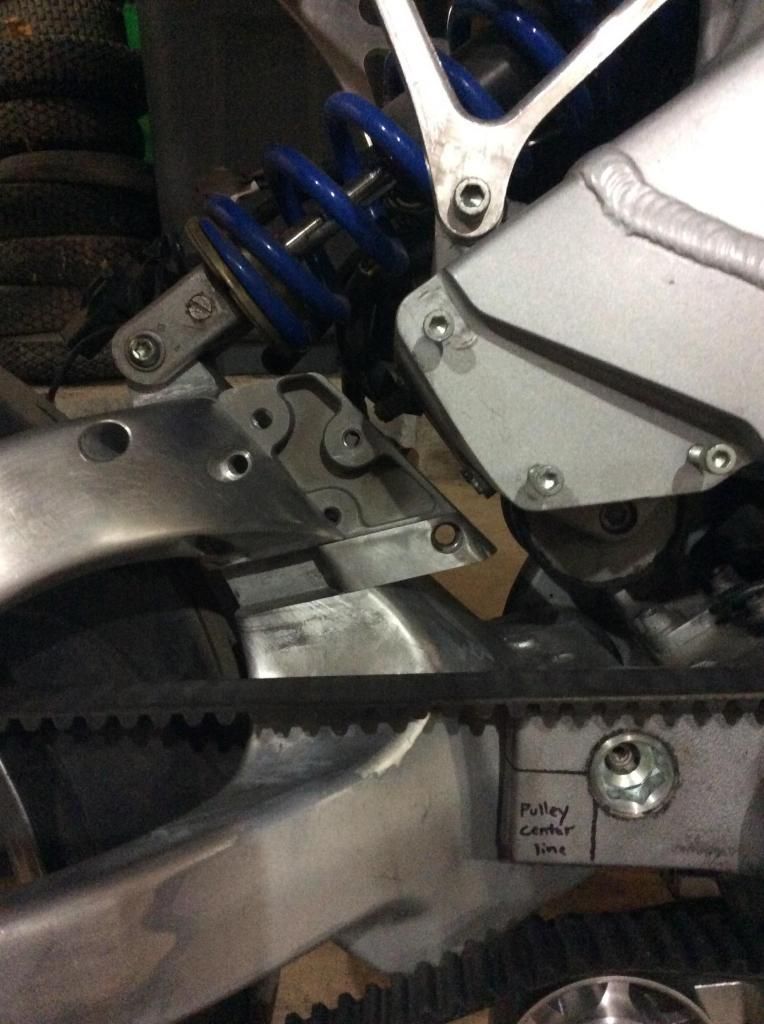 |
   
Truckinduc
| Posted on Sunday, December 28, 2014 - 04:08 pm: |
|
Forgot to mention, stock swingarm showed 16 lbs on my old scale. New swingarm showed 14 lbs. not sure how I cut that much weight out of it but I'm not complaining. |
   
Teeps
| Posted on Sunday, December 28, 2014 - 04:56 pm: |
|
Nice... I can sleep now knowing the belt can be fitted. Is that a custom belt idler wheel? Along that line; has anyone tried using a large skate wheel? |
   
Truckinduc
| Posted on Sunday, December 28, 2014 - 05:47 pm: |
|
Yes I made the idler wheel. I posted it about two weeks back. I wouldn't use a skateboard wheel for 2 reasons. First it will spin extremely fast. I doubt the small bearings could handle the rpm. So you would have a falure quickly. Second the belt will be bent tighter around the smaller wheel which will damage the belt internally and cause it to fail prematurely. I think I've found the max safe small diameter of the pully. |
   
Truckinduc
| Posted on Sunday, December 28, 2014 - 05:54 pm: |
|
Stealing the caliper off one of my ducatis to start my new caliper mount. Draining all that illegal blue brake fluid.
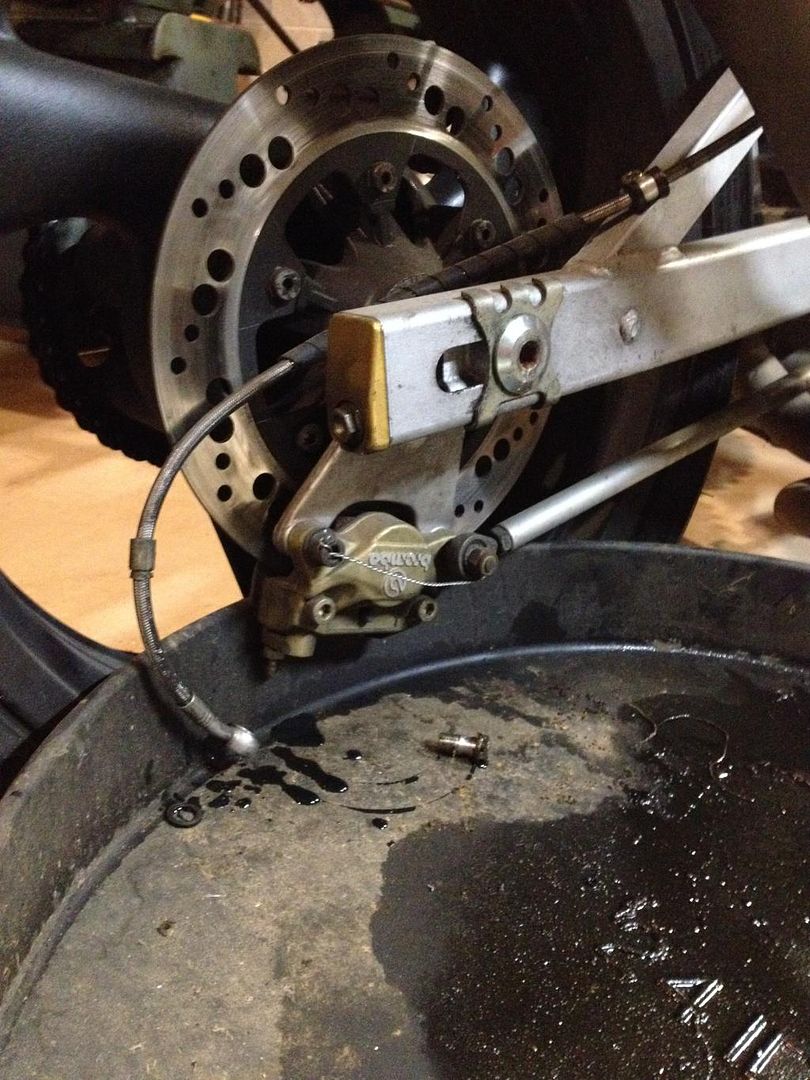 |
   
Truckinduc
| Posted on Monday, December 29, 2014 - 01:18 am: |
|
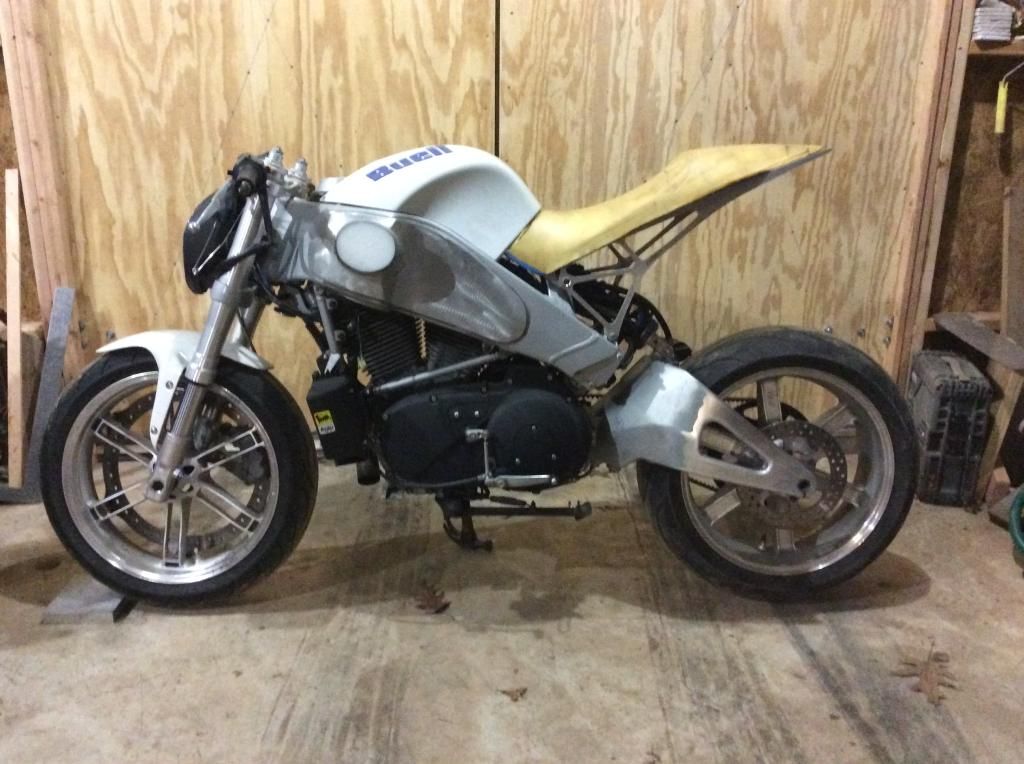 |
   
Beache
| Posted on Monday, December 29, 2014 - 08:26 am: |
|
Sweet custom kickstand. |
   
Greg_e
| Posted on Monday, December 29, 2014 - 10:24 am: |
|
You can get skate wheels up to 110mm diameter, but the bearings are not up to the task. They are only little 608 bearings. |
   
Truckinduc
| Posted on Monday, December 29, 2014 - 08:54 pm: |
|
Yes but why would you want to run a skateboard wheel? What's the advantage? |
   
Truckinduc
| Posted on Tuesday, December 30, 2014 - 02:05 am: |
|
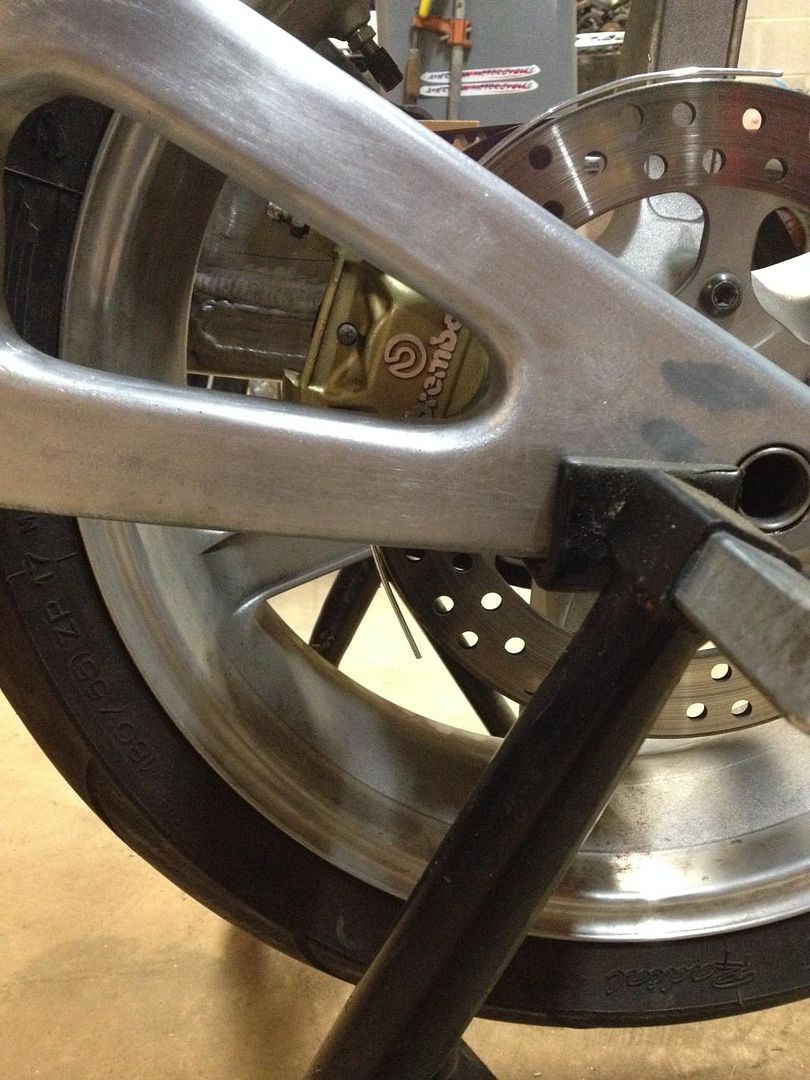 |
   
Teeps
| Posted on Tuesday, December 30, 2014 - 11:54 am: |
|
Truckinduc Posted on Monday, December 29, 2014 - Yes but why would you want to run a skateboard wheel? What's the advantage? Just a thought. The only possible advantage, such as it may be, would be availability & cost... that is if a skate wheel would work. And, from what you and others have said; would appear to be unlikely... Always thinking of alternative sources for replacement parts for the XB. Such as this: http://www.amazon.com/gp/product/B009OBP182/ref=pe _58340_124060110_em_1p_3_ti I believe this fan could be easily adapted for our XB motos. No, I have not tried the above fan. My thought would be to fit that fan (complete) within the original XB fan frame, as it appears to be proprietary. Again, just a thought. |
   
Truckinduc
| Posted on Wednesday, December 31, 2014 - 05:39 pm: |
|
Had to face the opposite side of the caliper mounts since I'll be using them backwards.
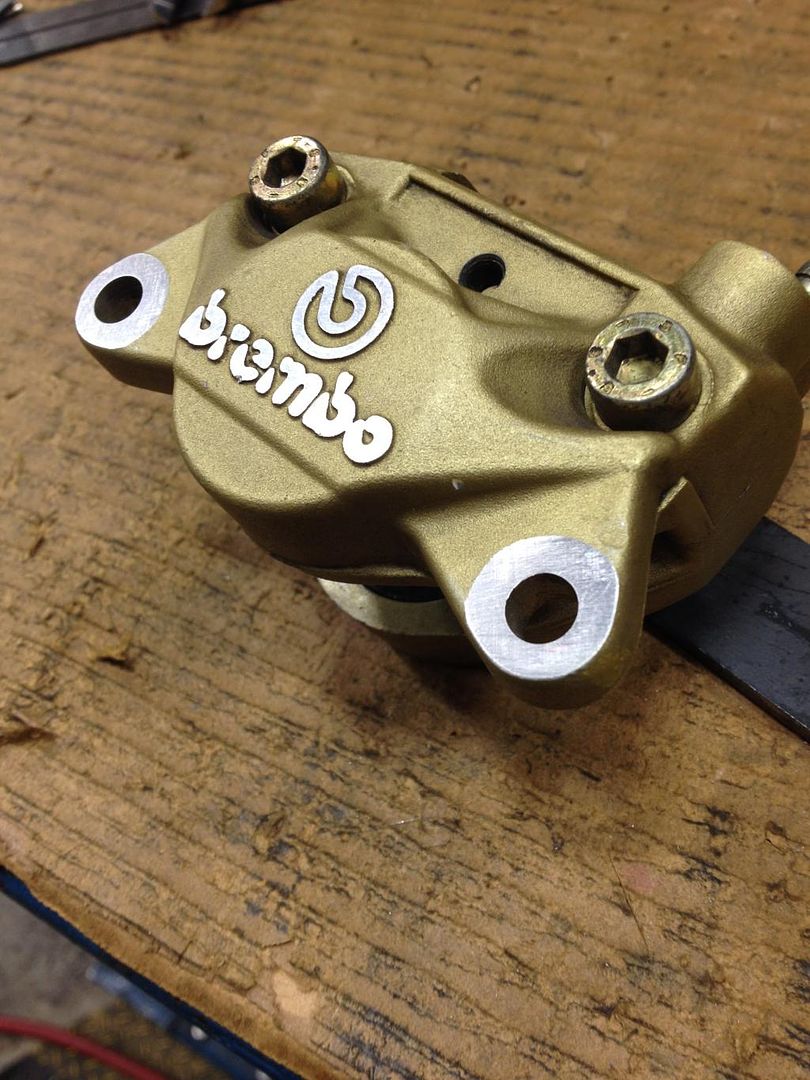 |
   
Truckinduc
| Posted on Wednesday, December 31, 2014 - 07:07 pm: |
|
Faced the caliper mount bosses and bottom tapped them. Then added the helicoils.
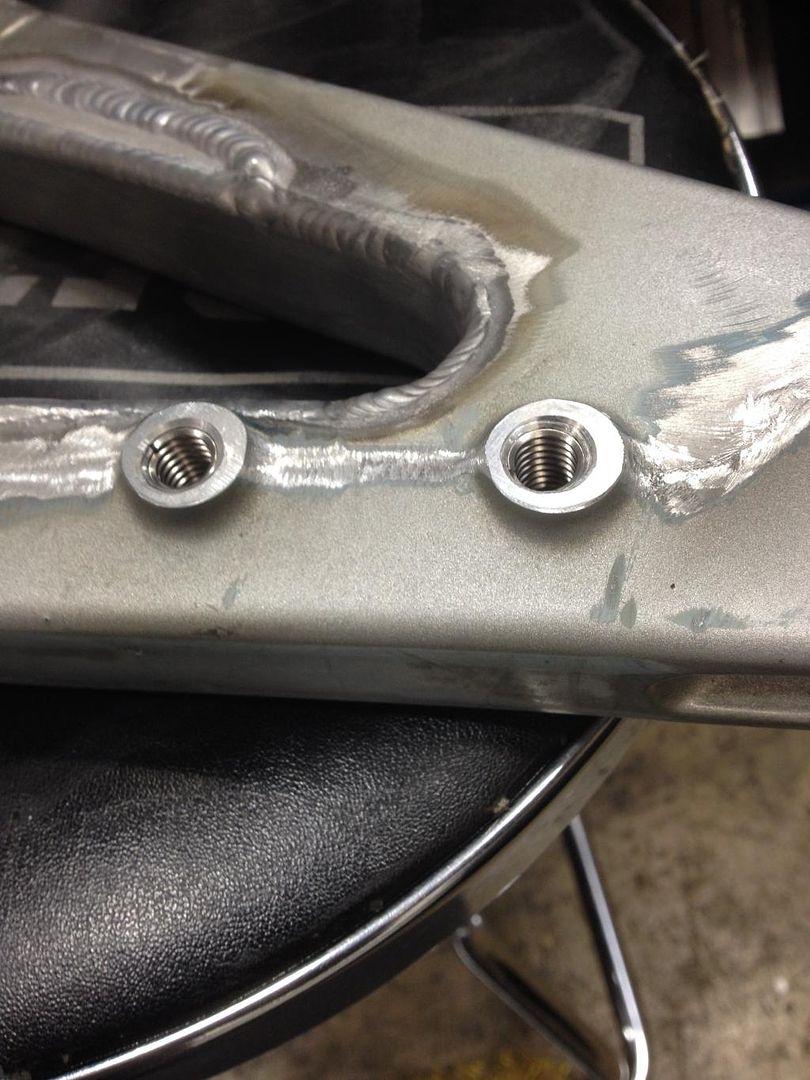 |
   
Ducbsa
| Posted on Thursday, January 01, 2015 - 07:00 am: |
|
Did the other side of the swingarm complicate access to face those bosses? |
   
Truckinduc
| Posted on Thursday, January 01, 2015 - 01:56 pm: |
|
Nah the other side didn't interfere with it. I clamped the axle in the vice with a parallel under it. Then I used a .750" endmill to face them. Worked great. You should see how complex machining my aprilia swingarm to fit a ducati, not that was a complex setup. [Img]http://i250.photobucket.com/albums/gg261/truckinduc/8134FAA3-21FC-4451-97B1-EF74FD4B63D6.jpg[/Img] (Message edited by Truckinduc on January 01, 2015) (Message edited by Truckinduc on January 01, 2015) |
   
Truckinduc
| Posted on Thursday, January 01, 2015 - 02:12 pm: |
|
Made an axle tool because I was tired of the ghetto ass method I had been using.
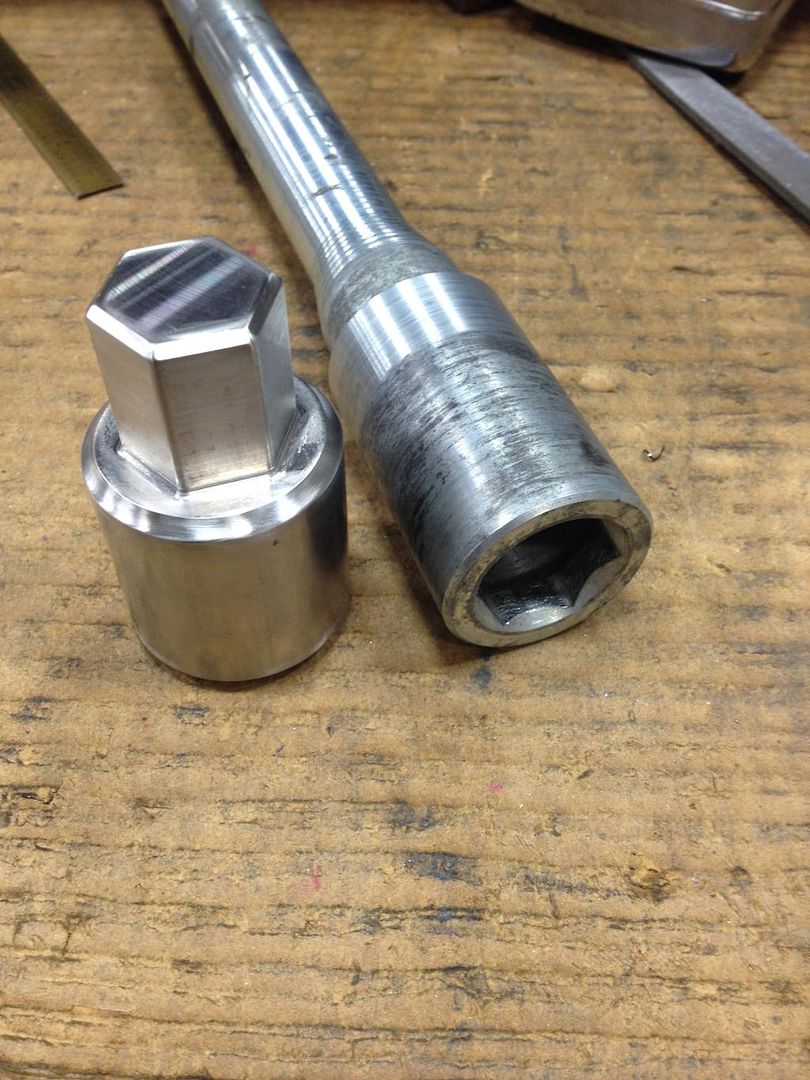 |
   
Greg_e
| Posted on Thursday, January 01, 2015 - 07:43 pm: |
|
I need to make one of those sometime in the near future. Looks like you are making an adapter to hold the caliper, why not just weld new mounting areas into the correct positions and bolt the caliper directly to them? (Message edited by greg_e on January 01, 2015) |
   
Truckinduc
| Posted on Thursday, January 01, 2015 - 09:57 pm: |
|
So this is a quick recap of how I designed my caliper mount. Mind you this is not the real mount. I made this for the sole purpose of measuring the hole locations. There was no other way to do it. First I made these individual pieces, one bolts to the caliper, one bolts to the swingarm.
This is a trick I like to use. I apply air pressure to the caliper once I get it in the position I want it. I use welding filler rod to space it from the outer edge of the rotor. The air pressure locks it In position.
Then it's as simple as welding the two pieces together.
Which left me with this
Now it's as simple as measuring the hole to hole locations to design the actual mount.
Now I just have to make the real one. About 3 hours of work for a few simple measurements. |
   
Truckinduc
| Posted on Thursday, January 01, 2015 - 10:01 pm: |
|
Looks like you are making an adapter to hold the caliper, why not just weld new mounting areas into the correct positions and bolt the caliper directly to them? That's a good question. At this point that would have been the easiest option. There is still a chance I might do just that. } |
   
Ducbsa
| Posted on Friday, January 02, 2015 - 06:02 am: |
|
"I clamped the axle in the vice with a parallel under it. Then I used a .750" endmill to face them." I see, you reached in from the top. Me not being a machinist at all, I assumed the swingarm was on its side. Thanks. |
   
Greg_e
| Posted on Friday, January 02, 2015 - 12:16 pm: |
|
Seems like there could be a lot of torque in the wrong direction for those swingarm bolts, I'd be concerned about vibration from the "free" end of that mount. But I like your trick to figuring the mount out. I think with all the other work you've done, welding in some round stock to mount the caliper would look cleaner. |
   
Truckinduc
| Posted on Friday, January 02, 2015 - 01:30 pm: |
|
Seems like there could be a lot of torque in the wrong direction for those swingarm bolts, I'd be concerned about vibration from the "free" end of that mount. But I like your trick to figuring the mount out. I think with all the other work you've done, welding in some round stock to mount the caliper would look cleaner. I agree with you. The stock mounting bosses are in a about the least ideal place now that the caliper is in the 9 o'clock position. I think I'll go ahead and shave the rest of the stock bosses down and attempt to remove the helicoils. Then make new studs and weld them in place. The bolt holes in the bracket turned out to be a little too close for comfort anyway. |
   
Greg_e
| Posted on Friday, January 02, 2015 - 07:54 pm: |
|
Can you tell that when I make things I fail a lot? I can't count the number of times I get half way through something just to chuck it in the bin and build it a different way that might be better. I will say that I'm really jealous of the machine tools you have to make things! Someday maybe I'll have a real machine shop so I can progress with my self studies. People like you make it seem so easy, only great skill can make the difficult seem this way. I'd love to see what you could come up with for a no welding repair for the transmission cover when the lips break off at the clutch. I'm certain there is a good way to fix this that the common person at home with common tools could fix. |
   
Ducbsa
| Posted on Friday, January 02, 2015 - 09:00 pm: |
|
Maybe adapt some of this: http://www.badweatherbikers.com/buell/messages/384 2/282980.html |
   
Truckinduc
| Posted on Saturday, January 03, 2015 - 04:44 pm: |
|
Changed my mind about mounting the caliper. No more adaptor brackets or that stuff.
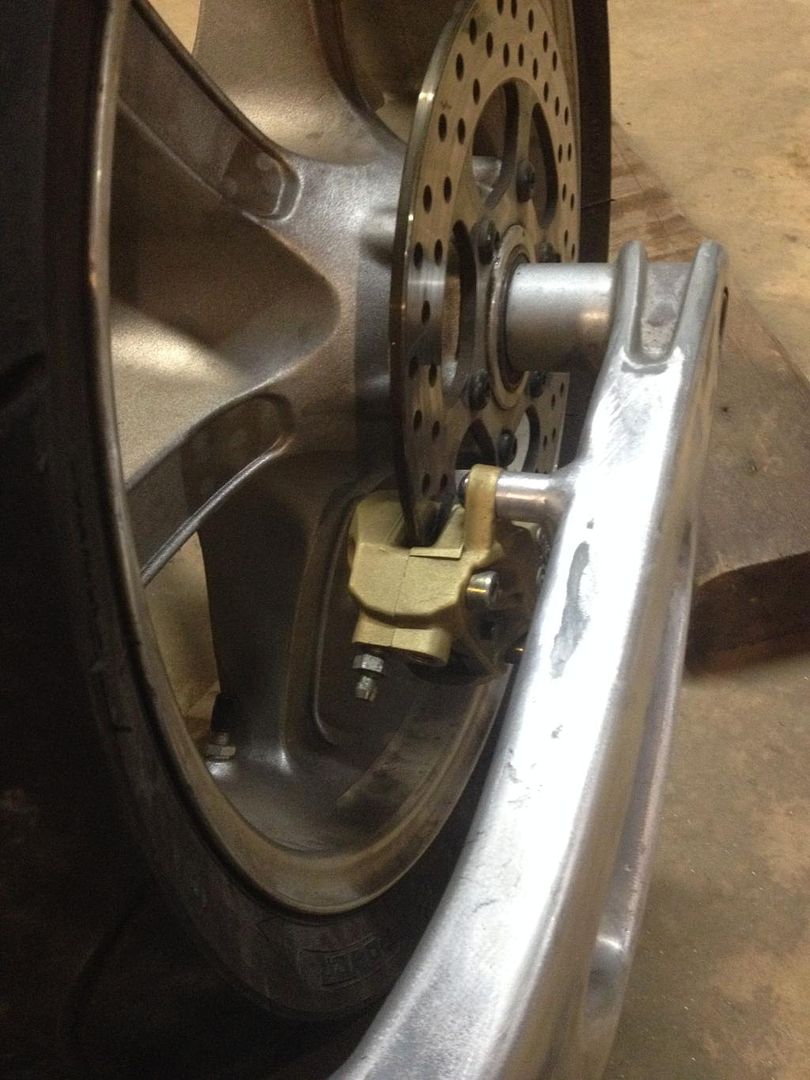 |
   
Teeps
| Posted on Saturday, January 03, 2015 - 05:31 pm: |
|
Much cleaner; hope it holes up... |
   
Greg_e
| Posted on Saturday, January 03, 2015 - 07:15 pm: |
|
That will look great when you get the paint on there. |
   
Truckinduc
| Posted on Saturday, January 03, 2015 - 07:56 pm: |
|
99.9% of the people who see it won't realize near the amount of effort involved in the swingarm alone, but I hope a few people do. I've got over 35 hours of work in the swimgarm, and it's almost done. |
   
Blake
| Posted on Sunday, January 04, 2015 - 01:01 am: |
|
Welded aluminum alloy and high cycle fatigue, the stress analyst's nightmare. At a minimum, I'd strongly advise a good re-heat treat and a professional shot peaning at all stress risers. |
   
Truckinduc
| Posted on Sunday, January 04, 2015 - 02:19 am: |
|
Are you speaking about the caliper mount or the swingarm in general? The caliper mounts will be gusseted to spread the load out. The swingarm in general will be given 4 months to age harden. I'll manually smooth all the stress risers (that I'm aware of). I'm not sure how much strength will be gained in the 4 months. Last time I got a quote for heat treating a single swingarm it was north of 1500$. I tried to minimize any stress risers in the initial design. Nice big internal radius's. I've never seen aluminum shot peened, is it common? I plan on sand blasting it but I know that does nothing for strength like shot peening. |