Author |
Message |
   
Gamdh
| Posted on Thursday, August 21, 2008 - 04:01 pm: |
|
I didn't trust my meter.. so I had a friend bring his over (much better quality) and was pretty much the same. In general, is was reading about 2/10 higher than mine. As for the ground to the VR.. don't really know for sure... How would I check it? |
   
Lost_in_ohio
| Posted on Thursday, August 21, 2008 - 06:50 pm: |
|
Mounting screw on the VR to the battery ground on the ohm setting on the meter. It should be zero a couple of hundredths of an ohm. |
   
Gamdh
| Posted on Thursday, August 21, 2008 - 07:42 pm: |
|
Hmmmm Ok I put one lead on the the screw (actually tried all 3) and the other on the battery ground. It reads .6 I also did the stator check. One lead on the screw on the case and the other lead testing each socket. It also reads .6 (manual says it should show 0 or its a grounded stator.) Also checked pin to pin continuity accross the stator sockets... it read about .6 (manual says is should be .1 to .3) So the manual says if the ohm meter does not read 0 with the leads shorted togehter than subtract the lowest value to resistance value of the stator. when I put the probes together is bounced around between 0.0 and .4 ( but for the most part it was .2 to .4). So.. I'm guessing this is not good, but am really confused. Now what? (Message edited by gamdh on August 21, 2008) (Message edited by gamdh on August 21, 2008) |
   
Reepicheep
| Posted on Thursday, August 21, 2008 - 10:40 pm: |
|
If you got .6 ohms from any stator pin to ground, you have a well and truly toasted stator. Sorry Does the manual say it should show 0? Or show infinity? It should show infinity, or it is a grounded stator. Meaning you have a grounded stator. Does the primary fluid stink? Pop off the derby cover and take a whiff... thats a dead giveaway. No idea how it was generating 17 volts in that state though... |
   
Gamdh
| Posted on Friday, August 22, 2008 - 12:19 am: |
|
It read .6 and the meter probes grounded to themselves were .3... so really its .3.. but still not good on that test. I guess the manual does actually say infinity.. which is not what I was reading. Will check the smell tomorow night. So, how hard is it to replace a stator?? Thansk!! |
   
Reepicheep
| Posted on Friday, August 22, 2008 - 05:29 am: |
|
Depends on how you look at it. Nothing particularly hard about it, but you have to remove the shift assembly, then primary cover, then the crank and countershaft nuts. That last step is maybe the fussiest, you will probably need special sockets, and have to lock the two primary sprockets with a spare chunk of aluminum cut to size. Then you just take off the stator bell, primary chain, and clutch pack as a unit, and the stator sits right there held in by 4 allen bolts. You will need new primary fluid, I think people have had decent luck re-using the new metal primary gaskets, but leaks are a hassle so I would probably just use a new one if I was going to be near a dealer anyway. The crank nut torque was updated from what the manual says, it is here in the knowledge vault somewhere. It goes on tighter now. I think the manual calls for loktite red. You can check the adjustment of that shifter pawl while you are in there. So not a huge deal, but you will probably need a new socket or two, and some scrap aluminum bar. |
   
Jlnance
| Posted on Friday, August 22, 2008 - 06:54 am: |
|
and some scrap aluminum bar Steel works better. The torque spec I believe (check me on this) is 260 ft-lbs. That is a huge amount of torque, and I know people who have crushed several home made locking tools. The $29 Jims tool that American Sport Bike sells doesn't seem so expensive after that. I think there is a retaining ring you need to remove to get the clutch pack off, so you'll need retaining ring pliers if you don't have a set. As Reep says, there isn't anything that is particularly difficult about this. But there were more non-difficult steps than I realized. If you have ever wanted to do the XB9 primary conversion, now is the time. |
   
Reepicheep
| Posted on Friday, August 22, 2008 - 08:24 am: |
|
Forgot about that snap ring... I do remember something one in there.
quote:There isn't anything that is particularly difficult about this. But there were more non-difficult steps than I realized.
Great quote! That about sums it up. It's the same with rocker boxes on a tuber... |
   
Gamdh
| Posted on Friday, August 22, 2008 - 08:24 am: |
|
Thanks guys! I did look at the SM.. it mentioned a few special tools etc. I'll probably give it a shot.. never done it, but thats never stopped me before. I'll make a list of everything I need (tools, gaskets etc...) The 260ft-lbs could be an issue.. don't have a torque wrench that big right now.... if I can't find a friend with one may be a good excuse to get one. |
   
Gamdh
| Posted on Friday, August 22, 2008 - 09:10 am: |
|
http://www.badweatherbikers.com/buell/messages/384 2/148030.html?1145912069 The previous torque spec was 190-210 Ft-lbs. The new Torque spec is 240-260 Ft-lbs. Man.. that seems like a lot!!! |
   
Red_chili
| Posted on Friday, August 22, 2008 - 10:03 am: |
|
See if you can't 'rent' a torque wrench for free from some of the auto parts chains. Pretty good program. They may not have one that goes that high though. 260 ft-lb. torque wrench would be 'spensive. Well, now, THIS looks handy! http://www.mysimon.com/9015-13550_8-26088261.html I guess $95 ain't TOO bad: http://www.northerntool.com/webapp/wcs/stores/servlet/product_6970_937613_937613 (Message edited by Red_Chili on August 22, 2008) |
   
Reepicheep
| Posted on Friday, August 22, 2008 - 11:03 am: |
|
I know the purists will shudder at this... but torque is torque. Tighten that nut till you start grunting. Take a two foot breaker bar ($10) and put it on the nut sticking close to parallel to the ground, maybe 15 degrees "upward". Move the pan of primary fluid onto a surface that is easy to clean. You will spill some on the next step, even if you relocate it to another state. It's a quantum physics thing, don't fight it. Use the following equation... be honest about your weight 260 foot pounds / Your Weight = X feet Put a piece of tape around the breaker bar to mark "X feet" from the center of the nut. Carefully put the center of your foot right on that tape mark, and gently lower your weight onto it, rotating the breaker bar maybe 15 degrees downward. Listen carefully, for the splash of the spilled primary fluid, just for fun. When it gets that far down, stop and reset the breaker bar to be 15 degrees or so up again. Repeat (no bouncing) until it stops turning. Be ***very*** gentle getting on the bar, act like you are trying not to break a branch suspending you over a big pan of primary fluid, and that you don't think will hold your weight I bet this will get you at least 90% accuracy, which is probably twice as accurate as you need it. And at this torque setting, I doubt any hand tool will get much better then that. My apologies to craftsmen everywhere... be thankful you don't know how I resurfaced the head on my KLR-250.
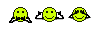 |
   
Jlnance
| Posted on Friday, August 22, 2008 - 12:45 pm: |
|
Man.. that seems like a lot!!! This dude could just barely make the wrench click:
I'll share with you one of his tips for doing this job. Get 4 long bolts with the same thread size primary cover screws (1/4-20 I think.) Cut the heads off the bolts. When you are trying to put the primary cover back on, screw the 4 bolts into 4 of the primary cover screw holes. Then slide the gasket on over the bolts. Next slide the primary cover on over the bolts. Put the primary cover screws into the remaining bolt holes, then remove your bolts, and replace with the screws. This vastly reduces the amount of fussing with the gasket that you must do. |
   
Gamdh
| Posted on Friday, August 22, 2008 - 12:48 pm: |
|
nice!! even I can handle that...
 |
   
Gamdh
| Posted on Saturday, August 23, 2008 - 02:58 pm: |
|
Question... the SM says you need a Spring Compressing Tool for the clutch diaphrahm Spring to be able to remove the retaining ring??? Do you really need that?? |
|