Author |
Message |
   
Sifo
| Posted on Monday, September 24, 2018 - 07:32 pm: |
|
TIG is easy to suck at!  |
   
Greg_e
| Posted on Monday, September 24, 2018 - 08:56 pm: |
|
Got the majority of the pieces cut, still need to work on some of the fit up.
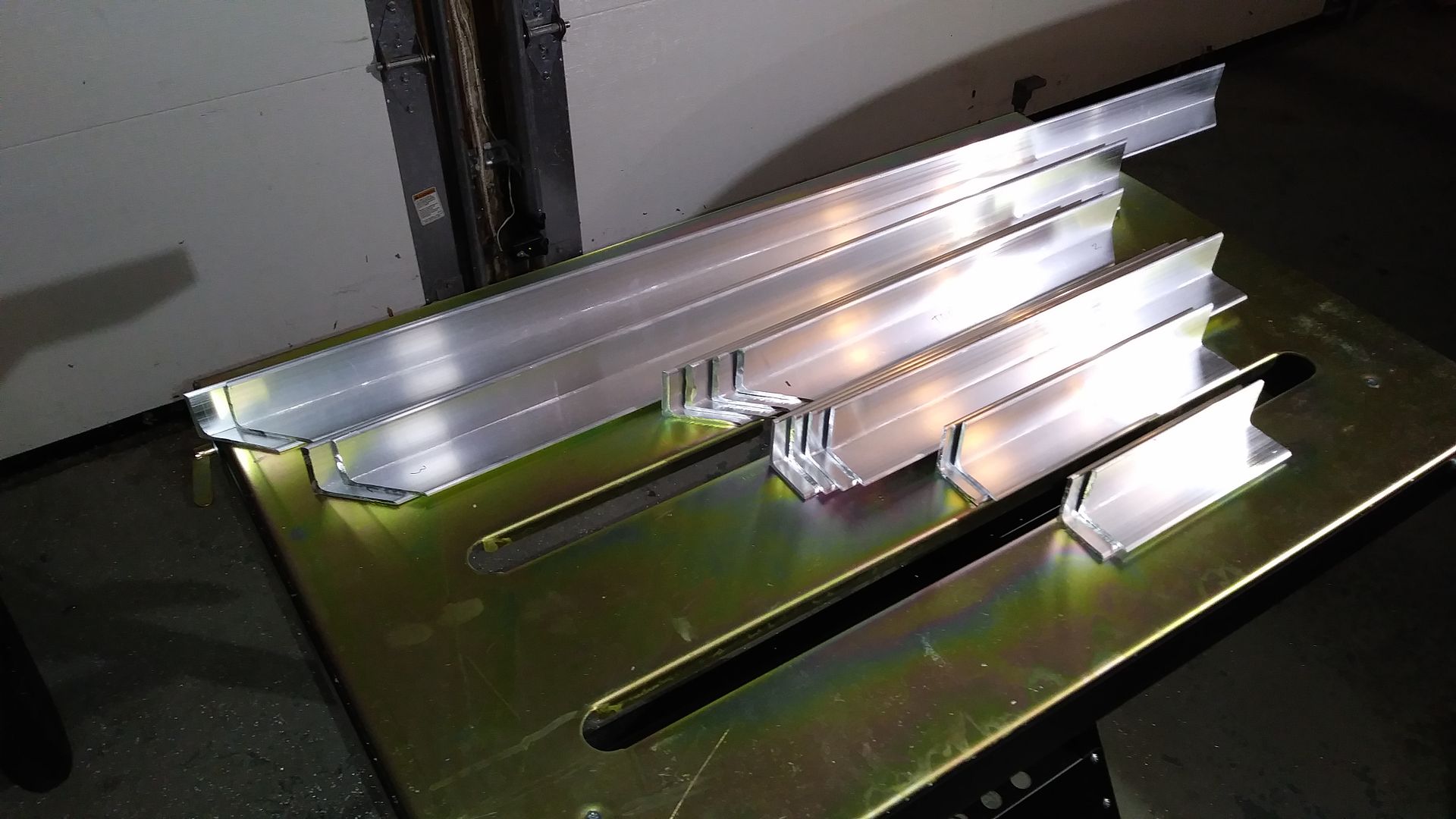 |
   
Figorvonbuellingham
| Posted on Tuesday, September 25, 2018 - 09:09 pm: |
|
This is the biggest bang for your buck right here.... https://www.amazon.com/AHP-AlphaTIG-Stick-Welder-W ARRANTY/dp/B076BSD6PG?crid=1EZSSK419E46N&keywords= tig+welder&qid=1537924051&sprefix=tig+wl&sr=8-5&re f=mp_s_a_1_5 And if you just need DC tig this is one hell of a little unit. I use it more then my AHP. Sadly the price has gone up considerably. Maybe tariffs? I gave around$180 for mine. https://www.amazon.com/Ansen-Welder-Inverter-Electric-Portable-TIG-205S-200A/dp/B07GNKR7LC?keywords=ansen+tig+welder&qid=1537924240&sr=8-2-fkmrnull-spons&ref=mp_s_a_1_fkmrnull_2_sspa&psc=1 (Message edited by figorvonbuellingham on September 25, 2018) (Message edited by figorvonbuellingham on September 25, 2018) |
   
Greg_e
| Posted on Tuesday, September 25, 2018 - 10:03 pm: |
|
Not a great night of welding, gave up after getting things tacked together. Took this many electrodes to get there and some seriously ugly welds.
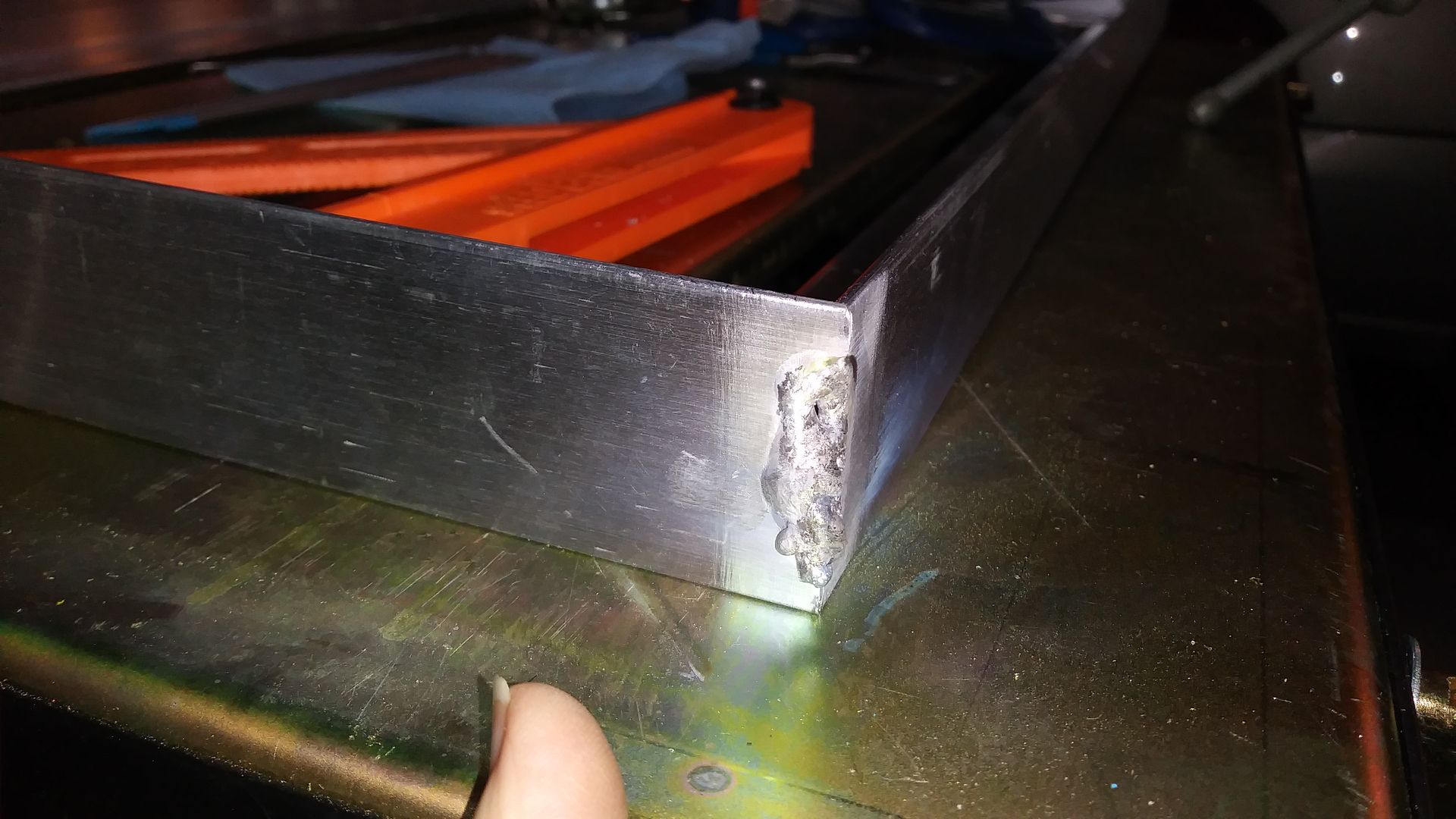 |
   
Tootal
| Posted on Tuesday, September 25, 2018 - 11:22 pm: |
|
I TIG'd a lot of stainless at the brewery and was pretty decent at it. Aluminum was just something we didn't use much in the brewing industry. One of my fellow machinist could TIG aluminum pretty well. I never tried but he always said to use AC and high frequency on all the time. Start until you see the puddle and then keep moving the puddle along as you add filler rod. I heard him train the younger guys but I never tried since my eyesight already sucked! |
   
Greg_e
| Posted on Wednesday, September 26, 2018 - 09:25 am: |
|
From what I've gathered, you can use a little lower current if you lower the frequency. I had this running the outside corners at about 85 amps with about 25% cleaning (positive polarity duration), it's 1/8 thick and many of the welds came out OK for my skill level. What that picture doesn't show is the black speckles and crap in it. Obviously I didn't clean it well enough. Going to need to grind most of that out and fix it, but that can wait until I have everything tacked together. A bunch of the butt welds inside picked up some crud, my fit up is fairly poor and I think it pulled some metal off the table. It's a galvanized table so I may need to fix it by grinding the zinc off or using mild acid to eat it away. The electrodes with massive blobs was just lack of dexterity and actually getting a blob of filler on them. I'll get there eventually, just going to take practice. Might change to the flex head torch I bought (like $10, who could resist), that might help get the arc into position better. Going to try and tack the uprights on tonight, unless laundry needs to be done. Using a drier plug to NEAM 6-50 adapter for power and 25 foot welding extension cable (fire insurance might not cover you unless you are using a cable designated as for welding use). |
   
Sifo
| Posted on Wednesday, September 26, 2018 - 10:06 am: |
|
Are you using a variable current control at this point? As things heat up, you really need to back off the current to keep things from going bad. Especially with thin stock like you are using. Otherwise you may have too start the weld kind of cool, and just go slow until it gets some heat soak. I see you've learned the fine art of welding your filler wire to the electrode!  |
   
Greg_e
| Posted on Wednesday, September 26, 2018 - 11:43 am: |
|
I started to use the variable control, but things weren't working right so I went back to 2t to just get this stuff tacked together. Most of these are just a dot or so of filler to keep it from cracking. That one corner fought me a lot. Kind of wish the welder would allow a 4t control with adjustable current in the welding phase. Yes, I'm getting really good at sticking the filler to the electrode. Even managed to weld the electrode, filler, and stick both to the base metal, those were fun to remove. |
   
Ourdee
| Posted on Wednesday, September 26, 2018 - 12:02 pm: |
|
Wish someone would write a twist of the wrist vol.2 for welding. |
   
Sifo
| Posted on Wednesday, September 26, 2018 - 12:20 pm: |
|
My first SS project...
 Just a couple of stair railings for my back deck.
 These, round to round joints tested me. Angles change real fast, and plenty of stuff to get in the way. It will work for it's purpose though. Ends are capped and rounded for a nice feel. I was trying to do a finish that involved seasoning linseed oil into the steel. After several hours, I've given up. I got some areas to come out really nice, almost black, but showing kind of a brownish red color. Either my lack of experience in this, or lack of a controllable heat source was causing problems though. All I have is a hand held MAPP torch. I need cooler, but broader heat. Too cool and it never seasons in. Too hot and it burns off and leaves you with bare steel again. It was a nice thought, but I need to move forward, so they will get painted black. Bare stainless just doesn't look right with the deck. At least I wont get rust streaks as the paint wears. |
   
Greg_e
| Posted on Wednesday, September 26, 2018 - 01:10 pm: |
|
Propane torch? |
   
Tootal
| Posted on Wednesday, September 26, 2018 - 01:20 pm: |
|
The nice thing about TIGing stainless is not matter how bad the initial weld is you can go back over the weld and make it pretty since the filler metal is already there, you just flatten out the peaks and you can make it pretty! BTW, if the weld has a brownish purple color you have the temperature correct. Just like any other trade, a good tradesman isn't one who doesn't make mistakes, it's the one that can fix his mistakes before the boss finds out! |
   
Sifo
| Posted on Wednesday, September 26, 2018 - 01:22 pm: |
|
A big propane torch, like those used for burning weeds out of driveways might have worked. I've got to get this project put to bed though, so I can get other projects done before winter sets in. I can always strip the paint off in the future if I find a way to make that finish work better for me. |
   
Natexlh1000
| Posted on Wednesday, September 26, 2018 - 03:59 pm: |
|
Here is a thing I just found about today: https://www.multiplaz.com/about It uses water!! I think it's a modern take of the Atomic Hydrogen thing above. |
   
Ourdee
| Posted on Wednesday, September 26, 2018 - 06:26 pm: |
|
I was looking at something years ago that used steam for shielding. Wonder if it was related. |
   
Fast1075
| Posted on Thursday, September 27, 2018 - 05:14 pm: |
|
First you have to learn to see wide. |
   
Greg_e
| Posted on Monday, October 01, 2018 - 09:03 am: |
|
So far the welder continues to work better than I do, but roughed out and tacked the frame of the cart. Still having problems with a few joints even after doing the same thing as other joints that work fine. Thinking I'm getting serious contamination from the galvanized welding table and I need a big plate of aluminum to put on top of the table.
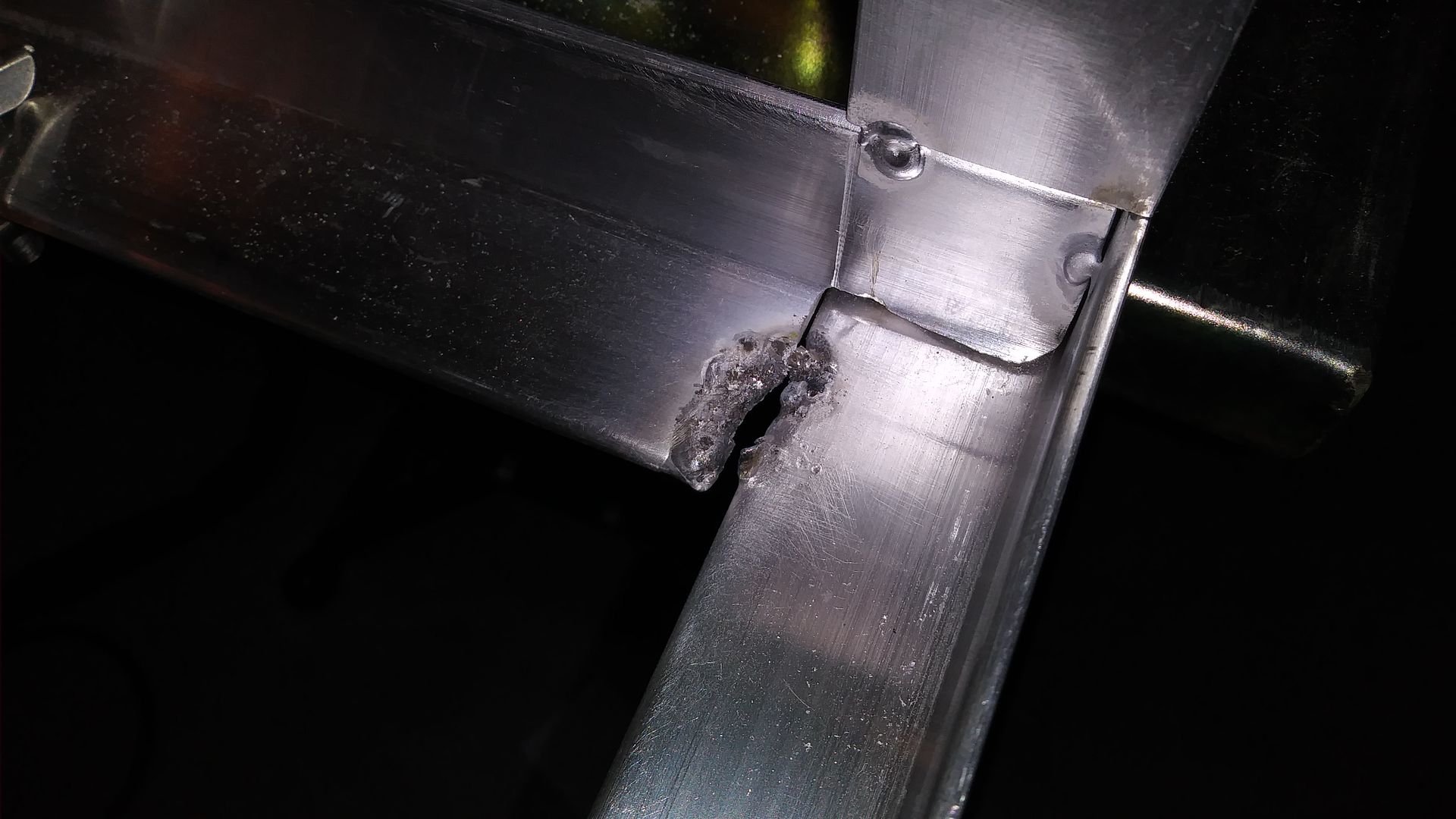 |
   
Fast1075
| Posted on Monday, October 01, 2018 - 09:15 am: |
|
New aluminum has a coating of aluminum oxide that must be brushed off. Otherwise you get crappy welds. I spent a day helping on a project. I was the gofer. The welder was a master. He even had a brush technique where he insisted you have to brush with the grain of the metal. Voodoo perhaps, but his welds were flawless. He used to weld stuff for NASA, including titanium. Also check your shield gas flow rate. And barring other issues, sometimes shield gas is contaminated. |
   
Ourdee
| Posted on Monday, October 01, 2018 - 09:47 am: |
|
You may learn that there is science behind some VooDoo. There is a VooDoo sticker on a Class A surface on Lil Red. Most people never see it. But, it is there. |
   
Etennuly
| Posted on Monday, October 01, 2018 - 01:51 pm: |
|
Hey I can make a TIG weld look just like that! White fuzzy film too. Like maybe too much or too little or wrong gas? I'm using straight argon. I can MIG aluminum projects like that in minutes no problem. But sometimes I want to slow the weld process down to make pretty welds. |
   
Fast1075
| Posted on Monday, October 01, 2018 - 02:20 pm: |
|
I was working on a stainless project once. I could not figure out why it was going to crap. Clean metal, correct wire, tri-mix, etc. I called my master welder buddy for advice. He came by and took one look. "Bad gas" he said. Long story short, I got a "good" tank of gas on the third try. He said sometimes the bottles have the wrong residual gas in them and/or have the wrong decals. |
   
Greg_e
| Posted on Monday, October 01, 2018 - 03:38 pm: |
|
Some of the welds look really good for my ability, so I don't think it is bad gas. Running straight Argon because I never know if I'm going to be working aluminum or steel. Gas was from Praxair, only place in town that will sell you a tank, everyone else leases every size. Praxair has some blends for different metals and aluminum does have a special blend available. But when I had some joints that had poor fit up, and they were backed up by the plated steel table, I had a very difficult time with them. I think this is a problem with metal contamination from skidding around the weld table and then pulling that into the weld. Right off the bat that one was making an angry sound and I should have quit immediately and figured it out. Now I get to grind a bunch of garbage out, and practice running a bead on edge until I can fill the void. That joint may well support the back edge of the gas cylinder, so it needs to be decent. And starting off with really poor fit doesn't help. And all that said, I may buy a fresh hose for the gas, I have some suspicions about it since it is all sticky from break down or other possible contamination. Not sure if I'll be working on this again tonight, would like to but I know there is laundry that needs to be done. Since it plugs into the outlet for the drier there is a conflict. I should also mention that I'm using an AC Works adapter and extension. These are labeled by the manufacturer as "for welding" which can be important if you have a fire. I should also mention that my first cable had the jacket pull away from the plug. And email and copy of the receipt later and I had a new cable (2 days) and return shipping label (need to go to FEDEX tonight to drop it off). All said and done, I think it is a good brand and wish I had bought the 50 foot cable instead of the 25 foot. Price was very good consider what I've paid for smaller extension. Nema 6-50 on both end and Nema 6-50 to drier plug on a short adapter. You can make your own. but it would be difficult to do it for less money. Ordered from Homedepot and shipped to store for pickup. |
   
Tootal
| Posted on Monday, October 01, 2018 - 03:44 pm: |
|
So forgive me if I missed it, but I think you are worried about the ground of the table? The work sliding? It sounds like your ground is not good. Try attaching the ground to a C-clamp and clamp right on the part you're welding. |
   
Greg_e
| Posted on Tuesday, October 02, 2018 - 07:57 pm: |
|
I now get to see how good the warranty is on this welder, just outside of the first 30 days and three times using it. |
   
Ourdee
| Posted on Tuesday, October 02, 2018 - 10:18 pm: |
|
Keep us posted. |
   
Sifo
| Posted on Wednesday, October 03, 2018 - 10:00 am: |
|
Sorry to hear that. What gave up? |
   
Greg_e
| Posted on Wednesday, October 03, 2018 - 11:16 am: |
|
The torch switch connection is shorted inside the welder. Apparently this is a $5000 welder??? https://iwestore.com/collections/outlet-sale/produ cts/outlet-sale-tig-200p-ac-dc-digital-tig-welder I've looked inside, no filters on the fans, no coating on the boards, etc., etc. It is not a $5000 welder. I might suggest $1000 as it competes with the Vulcan, but not $5000 as it simply does not have the features that a $5000 Fronius will give you. Also it looks like my flowmeter was killing me. Sometimes it flows what you set, sometime about 1/3 of that flow. That might be why the weld sounded "angry" and gave me such grief then melted away in a big puddle of garbage. Need to complain about that too, but so far no email. Going to have to call this afternoon. (Message edited by greg_e on October 03, 2018) |
   
Sifo
| Posted on Wednesday, October 03, 2018 - 12:11 pm: |
|
Well, we all knew it wasn't a $5,000 unit. It's a shame it's already taken a dump though. Common with many electronics though. Run it hard when new, and if it survives, it may well survive for years. A failure is likely to happen fairly quickly. I will say that I've had a few welds look a lot like that last one you posted, that were from poor gas coverage. I didn't want to point to that being your problem though, just because I certainly don't have the experience to know that that IS your issue. It's certainly a potential source of your issue though. There can also be causes such as too much electrode stick out. That was my problem when welding an inside corner on square tubing. The flow meter would be an affordable fix to a quality one. I plan on ditching mine as soon as I find a need to back purge a weld. That will be time to upgrade to a duel flow meter. As far as picking up the coating from your welding table, I really have no idea if that may be an issue or not. You could back your weld with copper though. It shouldn't weld to the aluminum, and you can cut some scraps from copper plumbing scraps. Just cut the pipe open and hammer it flat. You may need some more pieces to shim the rest of your work piece off the bench the same amount, but should be cheap prevention, if that is an issue you're having. Good luck with the customer service! |
   
Greg_e
| Posted on Wednesday, October 03, 2018 - 01:11 pm: |
|
They called at lunch. Guy seemed to know about the problem and said I need to put a diode in series with the black wire. Oddly he said polarity didn't matter. That said, the problem happens when I unplug the molex connector on the board for that function, so I doubt a diode will fix it. Going to grab some diodes from my parts boxes and give this a try tonight while I wait for him to send me the official diode fix. Bet I need a control board. But at least they got back to me today, so that looks good. For back purging I kind of decided I would just rent a second tank and meter. Don't think I'm going to do enough of that type of work to care about owning a splitter or dual meter. And you'll use the gas at a much increased rate so having a second tank to supplement my already tiny 80cf tank would be a good thing. |
   
Etennuly
| Posted on Sunday, October 07, 2018 - 11:15 pm: |
|
I'm glad this thread happened. I welded something the other day that can only be oxy acetylene welded. I'm glad I found my torch kit and got in some practice. Any good muffler shop has someone who can gas weld. The muffler inlet pipe broke loose from the otherwise good muffler on my van. This material is not conducive to being electrically welded by what ever machine. It is aluminized, slightly corroded, thin, not able to be ground clean due to position. Pretty cool how the flame heat burns away the contaminants as you weld. Can't do that with TIG or MIG! |
|