Author |
Message |
   
Fresnobuell
| Posted on Wednesday, July 30, 2014 - 04:32 pm: |
|
The good news is the little broken piece with the threads can be welded back on, saving substantial work cutting, welding and tapping for a new bolt hole. The bad news is welding this close to a gas tank is on the no-no list for alot of welders. Any opinions on how to handle this? What about some epoxy to "glue" it back on? Rough surface of the cast aluminium seem ideal for bonding. How much stress does this mount really take? Am I fooling myself? What epoxy product would best suit this application? This is quickly becoming the biggest issue to getting my steed back on the road!
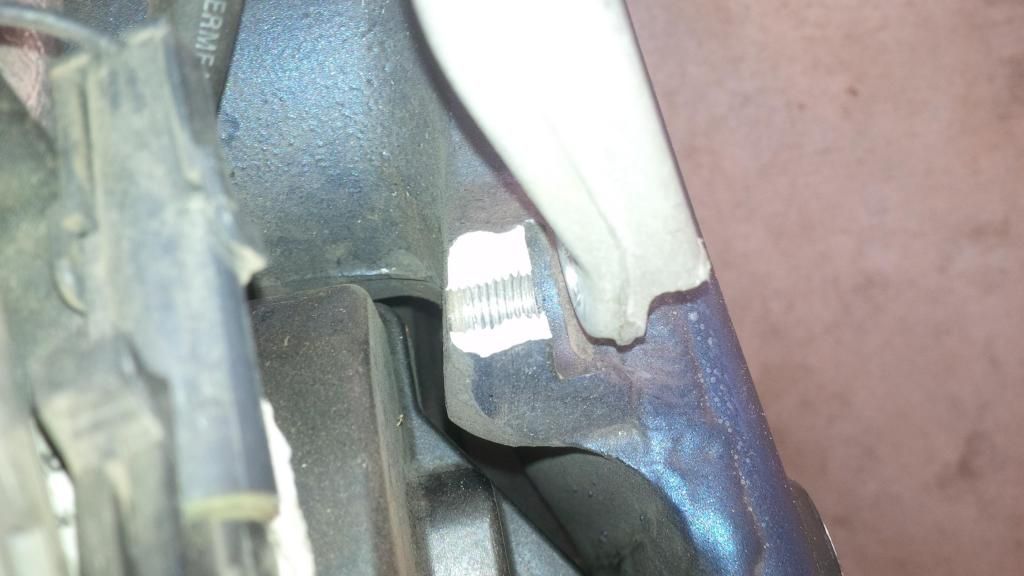 |
   
Oldog
| Posted on Wednesday, July 30, 2014 - 05:01 pm: |
|
Fresno if you can strip the bike and drain the tank, cap and fill with water total non issue the tank could be filled with fuel and that boss which is not on the skin welded then cooled. It should not present a problem, the gas tank explosion issue is due to sparks and vapors you can control the vapors by several means and I presume that you will use TIG welding. |
   
Fresnobuell
| Posted on Wednesday, July 30, 2014 - 05:51 pm: |
|
Oldog, I think i need to contact more welders. I was discouraged by the first two who wouldn't work near a gas tank. I read plenty of material online that makes it seem very doable. HOwever, I am wondering for some (alot?) people the "risk" isn't worth the reward ($$$) for such a small job. Also, I am trying to avoid dropping the motor. The rear jug is within an inch of the boss so I am hoping the heat doesn't hurt whatever material the top of the jug is made of. |
   
Nikoff90
| Posted on Wednesday, July 30, 2014 - 07:49 pm: |
|
If you are willing to Drive it up to the Bay Area you might try to get a hold of B_C on weldingweb or he could possibly point you in the right direction in Fresno. http://weldingweb.com/showthread.php?381781-Anothe r-can&highlight= (Message edited by nikoff90 on July 30, 2014) |
   
Nuts4mc
| Posted on Wednesday, July 30, 2014 - 10:04 pm: |
|
mine had the same type of break...it was welded and promptly broke - the material is NOT billet...it is some sort of casting ( sand casting...knowing HD cost accountants) a) cleaned up the area, ( no paint to grease or left over weld) (use acetone, lacquer thinner) b) I used JB weld and filled in the entire mount...I built some "dams" with wax paper and cardboard to keep the JB weld from flowing all over ( the wax paper keeps the JB weld from sticking to the cardboard) c) the bolt used to mount the sub frame is too big... causing a thin wall on that "lug" in the casting...and cracking and breaking ( HD must have had too many on hand and didn't want to throw them out) d) I used a 1/4-20 bolt all the way thru (I did not internally thread the repaired area) and some washers ( on each side of the through bolt) with a self locking nut...has been holding for 4+ years If you don't like the JB weld idea ...find a welder who can weld aluminum CASTINGS...have him add enough material ( rod) to fill in the tapped hole...then use a smaller bolt ( 1/4") like i did to help the repaired area survive hope this helps |
   
Nikoff90
| Posted on Thursday, July 31, 2014 - 06:04 am: |
|
Nuts it could be that the alloy needs post heat treatment it would be key to know what the actual material is for welding. Some aluminum has no strength after welding while some will actually gain strength, some materials will have no strength after welding but gain strength over time and need to be aged before being stressed. Weird stuff. |
   
Smoke
| Posted on Thursday, July 31, 2014 - 06:47 am: |
|
we've mig welded that boss multiple times on the race bike in place, battery disconnected, but what worked the best was to build up the broken area with weld, drill and bolt the subframe on with 1/4" boltand nut with large area washers. tim |
   
Fresnobuell
| Posted on Thursday, July 31, 2014 - 06:02 pm: |
|
smoke, I like your thinking. I just spoke to a welder that was more than willing to work in close proximity to the gas tank, but then when he saw the material (looks like cast aluminium) he said he couldn't work on it. SO, obviously I am not proficient at the types of welding (I have heard TIG and MIG, but have no idea what the difference is). Is it possible my welder can't do TIG and that's why he can't work on my bike? What I am getting at is if he's a MIG welder, perhaps he can work on the bike using your technique? PS, it's great hear from people who have had the same problem and found a solution. Thank you all. |
   
Nikoff90
| Posted on Thursday, July 31, 2014 - 07:59 pm: |
|
He may not have an AC tig welder or just may not be proficient in the process as it is difficult and specialized. I can tig cast aluminum but would and have paid top dollar to have someone better with the process to work on my motorcycle frames. Tig would be the top choice for what you need done. (Message edited by nikoff90 on July 31, 2014) |
   
Reepicheep
| Posted on Friday, August 01, 2014 - 08:25 am: |
|
It's also probably a "little upside and big downside" thing. They won't make that much on the job, and if the frame gets ruined, then the bike is effectively totaled. So anyone who has been burned before by somebody coming back at them when "stuff happens" won't go near that job. |
   
Fresnobuell
| Posted on Friday, August 01, 2014 - 01:09 pm: |
|
Nuts, I just re-read your post. I DO like the JB weld idea as it's a project I can take on myself. You say it's held up for several year. Great feedback. Any chance you can take a snapshot of your fix and post it? TIA |
   
Fresnobuell
| Posted on Friday, August 01, 2014 - 01:12 pm: |
|
quote:It's also probably a "little upside and big downside" thing.
I agree completely..then you throw in the fact it's on the gas tank and its some mystery cast aluminium material and it's no wonder I have gone thru 3 welders with no takers so far. |
   
Reepicheep
| Posted on Friday, August 01, 2014 - 01:58 pm: |
|
I wouldn't personally trust the JBWeld to hold, but might try it anyway as it is a fully reversible approach. It might work if the JB weld didn't do anything but keep the bolt centered, allowing the clamping force of two beefy washers on the remaining intact 60% of the boss to do the actual weight bearing. |
   
Nuts4mc
| Posted on Friday, August 01, 2014 - 02:45 pm: |
|
Fresno..here ya go...the frame boss by the VR was welded (by salvage yard I purchased the bike from...Insurance Co totaled it due to "cracked frame")...took the VR off to replace it and that's when I discovered the broken weld...you owe be a beer


|
   
Nuts4mc
| Posted on Friday, August 01, 2014 - 02:48 pm: |
|
Fresno...I used a 1/4-20 AHCS (allen head cap screw with a small OD washer) to fit inside the C'bore in the aluminum subframe:

 hope this helps (Message edited by nuts4mc on August 01, 2014) |
   
Fresnobuell
| Posted on Friday, August 01, 2014 - 03:57 pm: |
|
Yes I do. A virtual beer will have to do for right now.
Thank you for the pictures. So your situation was a cracked re-weld of the boss and you used JB Weld to completely fill in everything? Then you drilled the hole for the bolt in the JB Weld? |
   
Nuts4mc
| Posted on Friday, August 01, 2014 - 04:16 pm: |
|
Fresno...yes you are correct...I don't remember (it was back in 2010) but the large washer ( see top view ...looking down...between aluminum subframe and repaired boss)) may have been "glued" to the broken boss as well...it provided stability and support for the pieces and a "dam" for the JB weld as well - if you do the same "trick" make sure to roughen the surface of the washer (80 grit sandpaper/emery cloth)...the hole was completely filled...the washer provided a "pilot/guide" to drill the hole thru...you may want to do the same "trick" to BOTH sides of your broken piece...a SS fender washer works well...you'll need to grind a "flat" on one side (edge?) of the washer ( looking like the letter "D") to get the alignment close/correct...Ahhhh...that beer was great - 100 degrees down here today with 80% humidity..reminds me of my summer days back in Cleveland! (Message edited by nuts4mc on August 01, 2014) |
   
Fresnobuell
| Posted on Friday, August 01, 2014 - 05:12 pm: |
|
I have been doing some research on JB Weld online and I think I am going to use JB WELD to "glue" the broken piece back on, then get 2 washers and "glue" them on both sides of the boss for reinforcement. Finally, using the recommended bolt and locknut with probably 2 more washers. We will see.....at least I know the tank's not going to explode with this technique.
 |
   
Reepicheep
| Posted on Friday, August 01, 2014 - 05:27 pm: |
|
Not unless you smoke a cigar while you do it!  |
   
Skntpig
| Posted on Friday, August 01, 2014 - 07:27 pm: |
|
I have used JB weld quite a bit. Including the intake ports of a tuber head. Use a small drill bit or small dremel and chew into both pieces. Anything that the epoxy will contact. Dimple it like a golf ball and it will have much more surface to grab and hold. http://mototuneusa.com/MototuneF2Porting4.jpg |
   
Fresnobuell
| Posted on Friday, August 01, 2014 - 08:21 pm: |
|
quote:Use a small drill bit or small dremel and chew into both pieces. Anything that the epoxy will contact. Dimple it like a golf ball and it will have much more surface to grab and hold.
Yep, I love my Dremel! I use it all the time. thanks for the advice. I do plan to rough up all the surfaces for sure. |
   
Figorvonbuellingham
| Posted on Sunday, August 03, 2014 - 09:23 am: |
|
Personally Id rather have weld then epoxy. I wouldn't want to have epoxy fail at 65 - 160+ MPH. Seems a bit risky to me. I'd definitely find someone who would fill that tank with h2o and pile weld on there then grind and drill. If nothing else find a friend that has a wire weld and get some aluminum wire and a party tank of helium from Walmart. Youll get a much better weld with helium. This just comes from 30 years of metalworking though. I hope the epoxy works ok for you and you have a safe bike after. |
   
Torquehd
| Posted on Sunday, August 03, 2014 - 12:14 pm: |
|
One problem with welding is that the cross sectional amount of material under load is reduced. If you only weld the broken piece back on, the best you can do is lay a bead of weld all the way around the perimeter. The two broken faces, while touching, are not joined. Only the perimeter, where welded, is joined. One could compensate for this by welding a larger piece (of extruded stock) on the backside. You could even lay up several pieces of flatstock, ensuring a good weld from frame to flatstock, and from flatstock to broken tab. The other problem with welding is the issue of annealing. To my knowledge, regardless of alloy, aluminum that has been heated past solution temperature (say, 950-1,050 degrees, depending on alloy), will remain annealed until the internal crystalline structure recrystalizes. This process is sped up by conventional heat treating. Extruded aluminum, in particular, is extremely soft after heating to solution temp. It will be much stronger after sitting for a month. So, if this was my bike, I'd drain and purge the tank, remove and/or cover anything that could be damaged by the heat and splattering, and reweld the piece on. I'd build up the back side with some big, ugly pieces of flatstock, grind it smooth, and let it sit for 4-6 weeks before reassembly. |
   
Dannybuell
| Posted on Sunday, August 03, 2014 - 12:53 pm: |
|
or just start adding metal and then tap into a new hole? |
   
Figorvonbuellingham
| Posted on Sunday, August 03, 2014 - 03:09 pm: |
|
Or grind it all off and weld on a boss. |
   
Torquehd
| Posted on Sunday, August 03, 2014 - 04:35 pm: |
|
That's not a bad idea. I assume the frame is hollow at that location, and inside is the fuel tank. You'd have to be pretty careful grinding. If you had the resources, you could make a pattern and sand cast a new mount. You could also buy some thick flat stock, maybe 1" thick, and sculpt a new mounting tab using a dremel and a file and sandpaper. Welding the new piece on would probably require dropping the motor. The bigger the mounting perimeter, the better. But that could get hairy if that area is indeed fuel tank on the inside. If you don't have the means to weld Al, your best bet is probably to remove the frame, clean flush the fuel tank, and take it to a machine shop or a machinist buddy if you have one, and turn it over to them. |
   
Torquehd
| Posted on Sunday, August 03, 2014 - 04:37 pm: |
|
That's the upper subframe mount, right? |
   
Fresnobuell
| Posted on Tuesday, August 05, 2014 - 06:27 pm: |
|
Yes, upper sub-frame mount on the left side. Interesting ideas, fellas. Maybe I am being naive, but even if this epoxied tab breaks again, it won't be catastrophic as there are 3 other mounts... Then maybe I drop the motor and do it "right". The idea of taking some flat stock and creating a new boss to be welded on seems like a winner. |
   
Dannybuell
| Posted on Tuesday, August 05, 2014 - 11:28 pm: |
|
if you put a 45 degree bevel on all of the insides of the stock the welder will get a much larger purchase! |
   
Brokengq
| Posted on Wednesday, August 06, 2014 - 02:11 am: |
|
Fresno, any option that involves welding on a new boss is going to require dropping the motor, so be prepared for that. Tungsten, or TIG welding, requires a fairly large area to work in. MIG is a little more forgiving, but does not work well with most kinds of aluminum (in my experience MIG welding aluminum tends to damage the stock to some extent). A TIG welder is a fairly nice sized gun that super heats a core of tungsten within it. The heat is transfered via proximity to the metals being bonded. Long story short, you need room to get the TIG gun very close to the weld area, all the way around. If it were my bike, I would experiment with the options listed that involve a straight bolt-through first. The subframe isn't going to fly off due to one missing bolt (don't get me wrong, you'll feel it if it breaks). Try one idea, test, inspect, repeat until satisfied. Good luck. |
|